Flexible Screw Conveyor | Efficient Bulk Material Handling Solution
What is a Flexible Screw Conveyor?
A Flexible Screw Conveyor—also referred to as an inclined screw conveyor—is a highly adaptable and space-efficient mechanical conveying system used to transport dry bulk materials. It consists of a rotating helical screw inside a flexible or semi-rigid tube, capable of moving materials vertically, horizontally, or at an incline.
In manufacturing plants, warehouses, and processing facilities, this conveyor is indispensable for moving powdered, granulated, or flaky materials like flour, coffee, grains, plastic pellets, and more. It’s commonly integrated with a hopper, creating a complete inclined screw conveyor with hopper system, perfect for batch feeding and continuous processing applications.
Whether you’re working with a compact layout or dealing with awkward angles, the flexible screw conveyor fits into the most challenging plant designs—something rigid conveyors often can’t accommodate.
Common Materials Conveyed by Flexible Screw Conveyors
One of the biggest advantages of flexible screw conveyors is their ability to handle a broad spectrum of materials. Below is a list of commonly conveyed items, organized by industry.
Industry | Materials |
---|---|
Food & Beverage | Flour, coffee, rice, cocoa, sugar, spices |
Chemical | Powdered chemicals, detergents, catalysts |
Plastics | Pellets, flakes, powder resins |
Agriculture | Seeds, grains, feed, fertilizers |
Pharmaceuticals | Vitamins, supplements, powders |
Special screw designs like flat screws for sticky materials or cut-flight screws for fragile items enhance performance and material compatibility.
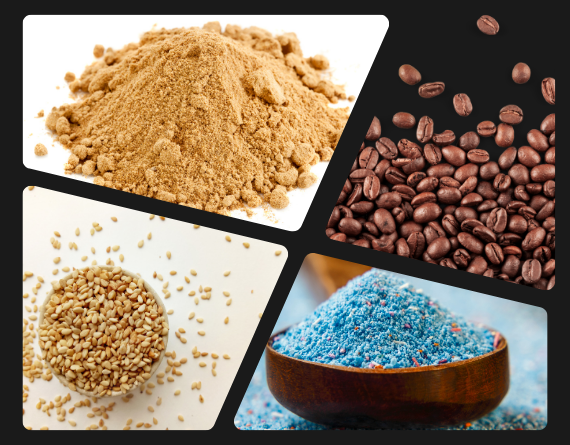
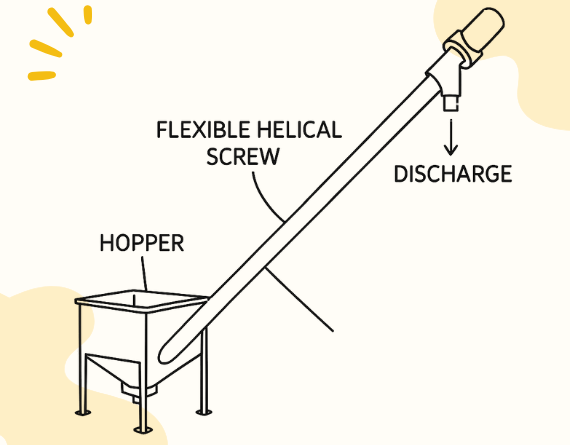
How Does a Flexible Screw Conveyor Work?
The principle behind the inclined screw conveyor design is rooted in simplicity and functionality. Here’s how it works:
Step 1: Material Entry
Bulk material enters through the hopper, either manually or via an automatic feeder. Hoppers can be custom-designed based on the material type and desired flow rate.
Step 2: Spiral Movement
Inside the tube is a flexible helical screw driven by a motor. As it rotates, the screw propels material along the tube’s path. The helical action moves materials without crushing or degrading them.
Step 3: Inclined Transfer
The screw’s design enables the conveyor to operate at various angles—up to 60 degrees. This flexibility in inclined screw conveyor design makes it ideal for elevation change without the need for additional vertical lifting equipment.
Step 4: Discharge
The conveyed material is discharged at the opposite end into the next stage of the process—whether packaging, mixing, or another storage vessel.
The enclosed system minimizes dust, protects material from contamination, and offers smooth, low-maintenance operation.
When Should You Use a Flexible Screw Conveyor?
You should consider a flexible or inclined screw conveyor with hopper when facing challenges like:
- Limited Floor Space: The flexible tube can route around machinery or structural obstacles without compromising performance.
- Material Elevation Needs: Perfect for moving materials vertically or at an incline without extra elevators or bucket lifts.
- Frequent Product Changeovers: Quick disassembly and easy cleaning make it suitable for industries with diverse product lines.
- Dust Control Requirements: Enclosed conveying reduces exposure to dust, maintaining workplace cleanliness and protecting operator health.
- Feeding into Mixers or Packaging Machines: When precise, consistent feeding is required, pairing the conveyor with a hopper ensures accuracy and controlled flow.
Whether you’re dealing with light powders, abrasive granules, or fragile flakes, the inclined screw conveyor provides a reliable, low-cost way to transport materials with minimal energy consumption.
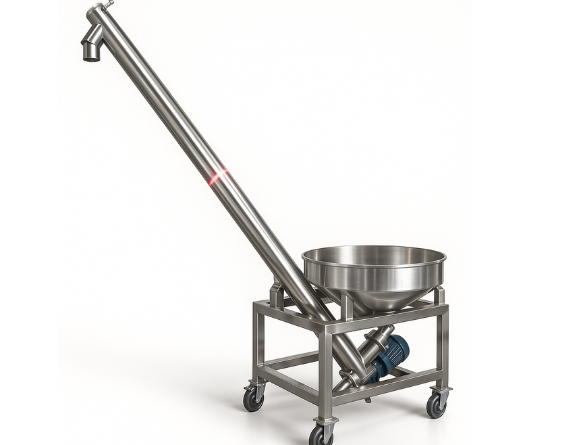
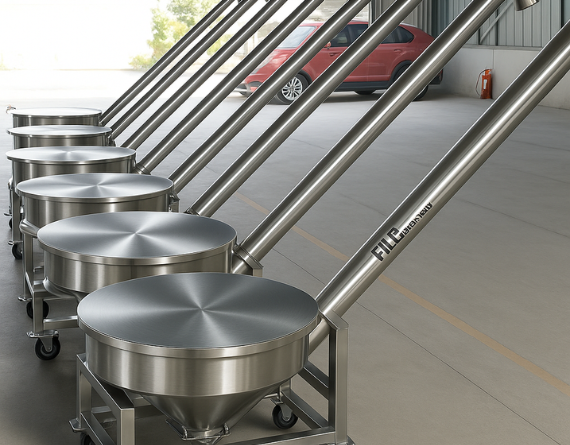
What Should You Pay Attention to When Using a Flexible Screw Conveyor?
While inclined screw conveyors are robust and efficient, attention to a few operational details ensures optimal performance and longevity:
-
Material Characteristics: Stickiness, moisture content, and abrasiveness affect flow and wear. Select the right screw type and tube material accordingly.
-
Inclination Angle: Excessively steep angles may reduce throughput. For very steep applications, custom screw geometries or multiple conveyors may be necessary.
-
Hopper Feeding: Ensure a consistent feed into the hopper to prevent surging or underfeeding, which affects material flow and accuracy.
-
Overloading: Avoid overloading the system, which can strain the motor and wear out the screw prematurely.
-
Maintenance Access: Design the system for easy disassembly and cleaning, especially in food-grade or sensitive material environments.
-
Static Electricity Build-up: When conveying powders, grounding the equipment can prevent static discharge hazards.
Design Considerations for Inclined Screw Conveyors
Creating an efficient inclined screw conveyor design goes beyond just choosing a tube and motor. Key factors to consider include:
1. Inclination Angle
Performance varies with the angle of incline. Typically, material flow efficiency begins to decline as angles exceed 45°, requiring adjustments in screw pitch or speed.
2. Screw Type and Pitch
- Standard pitch is ideal for horizontal or low-incline applications.
- Variable pitch screws help accelerate material into the system and are better for steep inclines or sluggish materials.
3. Tube Diameter and Length
The diameter affects flow rate, while the length determines the required torque. A longer tube at a steep incline requires more power to maintain flow consistency.
4. Hopper Size and Configuration
Larger hoppers reduce the need for constant refilling. The hopper shape and feeder design can also help regulate flow and prevent bridging or clogging.
5. Material of Construction
- Stainless steel for food and chemical resistance.
- Carbon steel for general applications.
- Polymer tubes for lightweight and non-abrasive materials.
Proper design ensures your inclined screw conveyor with hopper delivers maximum performance with minimal maintenance.
Not recommended. While it can manage some moisture, very sticky materials tend to clog or bind. In such cases, specialized screws and hoppers with agitators may help.
Typically, up to 60 degrees is feasible. However, as the incline increases, throughput decreases. Customized screw pitches and higher torque motors can help overcome this.
Most models are easy to disassemble. Simply remove the tube, screw, and hopper components. Many food-grade systems are CIP (Clean-In-Place) compatible.
They are quite energy-efficient, often operating with small motors ranging from 1–5 HP, depending on tube length, material type, and incline.
Absolutely. You can feed directly into mixers, packaging machines, or even pneumatic systems using discharge valves, sensors, and controllers.