Modular Belt Conveyor
Modular Belt Conveyors – Durable, Hygienic, and Built for Heavy-Duty Applications
What is a Modular Belt Conveyor?
A modular belt conveyor uses a series of interlocking plastic modules to create a continuous, flexible belt surface.
Unlike traditional fabric belts, modular plastic conveyors are made of rigid segments connected by rods, offering superior strength, durability, and ease of maintenance.
Related terms: modular belt conveyors, plastic modular conveyor belt, modular plastic conveyor belts
Applications of Modular Plastic Conveyors
Modular conveyor systems are widely used in industries where sanitation, durability, and load-bearing capacity are critical.
Common applications include:
- Food processing (meat, seafood, bakery, vegetables)
- Frozen food handling
- Beverage and bottling lines
- Packaging and secondary packaging
- Industrial parts conveying
Their design allows for:
- Wet or oily product handling
- Heavy or abrasive materials transport
- Smooth curves and elevation changes
Technical Specifications
Feature | Details |
---|---|
Conveyor Belt Material | PP,PE ,POM |
Belt Width | Customizable (Various standard options) |
Speed Range | Adjustable; up to 30 meters per minute |
Load Capacity | Up to 500 kg per meter |
Operating Temperature | -40°C to +90°C |
Drive Type | AC, DC, or Servo Motors |
Frame Construction | Stainless Steel, Aluminum, or Powder-Coated Steel |
Conveyor Length | Customizable to meet layout requirements |
How Modular Plastic Conveyors Work
Modular plastic conveyors employ a positive drive system, where interlocking plastic modules form a continuous belt propelled by sprockets. This design ensures precise tracking, eliminates slippage, and reduces maintenance requirements.
🔹 Positive Drive Mechanism
Unlike traditional friction-driven belts, plastic modular conveyor belts are driven by sprockets that engage directly with the belt’s underside. This positive engagement guarantees consistent movement, even under heavy loads or in wet conditions, and negates the need for tensioning systems.
🔹 Modular Construction
Each belt comprises individual plastic modules connected by hinge rods, creating a robust and flexible structure. This modularity allows for easy replacement of damaged sections without the need to replace the entire belt, significantly reducing maintenance time and costs.
🔹 Versatility in Design
The modular nature of these belts enables customization to accommodate various conveyor configurations, including straight runs, curves, inclines, and declines. This flexibility makes them suitable for a wide range of applications across different industries.
🔹 Material Selection
Modular belts are typically made from durable thermoplastics such as polypropylene, polyethylene, or acetal. These materials offer excellent resistance to chemicals, moisture, and temperature variations, making them ideal for food processing and other demanding environments
By leveraging the positive drive mechanism and modular construction, modular plastic conveyors provide a reliable, low-maintenance solution for various material handling needs.
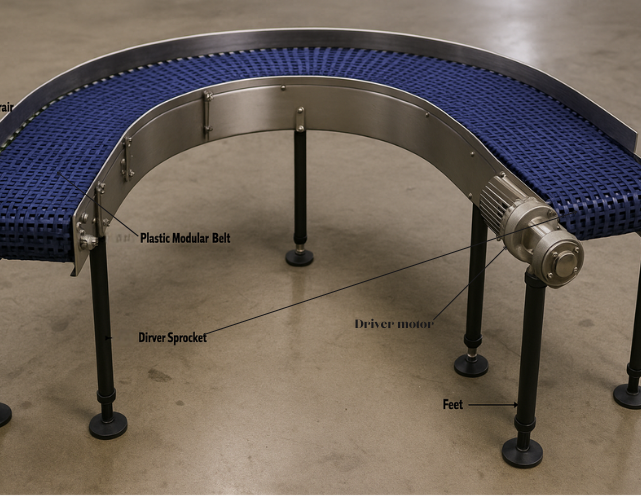
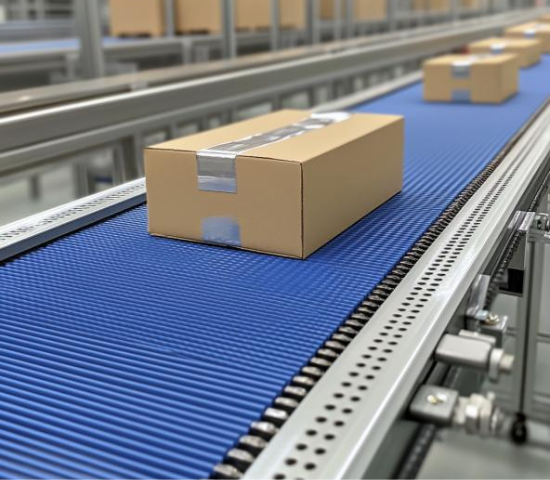
Applications of Modular Belt Conveyors
The versatility of modular belt conveyors makes them suitable for a wide variety of applications across different industries:
- Food Processing: Ensures hygienic handling and transportation of food products, meeting strict safety standards.
- Automotive: Perfect for conveying heavy vehicle components like engines, transmissions, and parts.
- Pharmaceutical: Provides safe, controlled movement of sensitive products through production and packaging lines.
- Packaging: Handles various package types, including bags, cartons, and bottles, on high-speed lines.
- Logistics & Warehousing: Streamlines the transportation of boxes, pallets, and containers in distribution centers.
Modular Plastic Conveyor Belt Types & Applications
Different industries and product types require specialized belt surfaces.
At Fill Package, we offer a variety of plastic modular conveyor belts, each designed for a specific function to optimize product handling, hygiene, and production efficiency.
Flat Top Modular Belt
- Features: Continuous, fully closed surface
- Applications: Ideal for general product conveying where support and stability are required.
Suitable for packaged goods, boxed items, trays, and uniform-sized products.
Provides a smooth ride with minimal vibration.
Flush Grid Modular Belt
- Features: Open grid structure for easy drainage and airflow
- Applications: Used in processes involving washing, cooling, draining, or drying, such as seafood, vegetables, and fruits.
Prevents water or debris accumulation on the belt surface, ensuring cleanliness.
Raised Rib Modular Belt
- Features: Raised ribs along the belt surface to maintain product alignment
- Applications: Helps guide products during transfers between conveyors or machinery.
Perfect for unstable or irregularly shaped items, preventing misalignment or jams.
Friction Top Modular Belt
- Features: High-friction surface inserts
- Applications: Designed for inclined conveyors, preventing product slippage on slopes up to 20 degrees.
Common in snack packaging, boxed goods, and small components needing elevation.
Roller Top Modular Belt
- Features: Integrated rollers on the belt surface
- Applications: Ideal for low-pressure accumulation zones, allowing products to queue without damage.
Used in buffer areas, sorting lines, and gentle product handling where pressure-sensitive goods need space.
Perforated Flat Top Modular Belt
- Features: Flat top with strategically placed perforations
- Applications: Balances airflow and water flow while offering a mostly closed surface.
Useful in cooling, drying, or processing lines requiring some drainage but better product support than flush grids.
These specialized modular conveyor components ensure that every product—whether slippery, fragile, or irregular—moves through your line safely and efficiently.
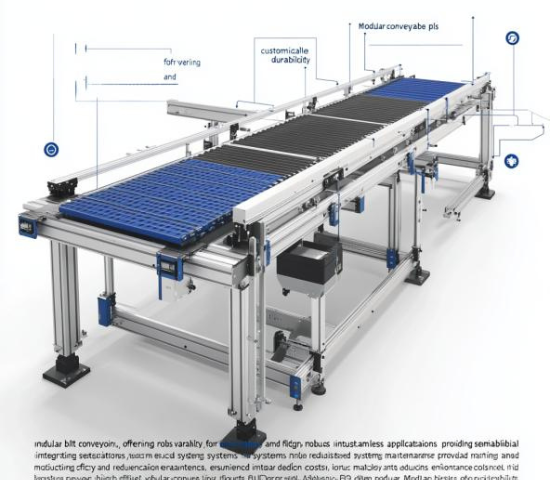

Key Advantages of Modular Belt Conveyors
Low Maintenance & Easy Repair
-
Damaged sections are replaced individually—no need to change the whole belt
-
Self-locking modules enable quick assembly/disassembly
-
Saves time, reduces spare parts costs
Versatile Applications
-
Handles wet, oily, heavy, or fragile products
-
Supports complex layouts with curves, inclines, sidewalls
-
Suitable for both primary production & packaging lines
Durable & Hygienic
-
Made from food-grade PP, PE, POM materials
-
Open hinge design allows for easy washdown
-
Longer lifespan than fabric belts in demanding environments
Anti-Slip Conveyor Belt | Solutions to Prevent Product Slippage
When transporting goods on inclined or reversed conveyors, preventing products from slipping or falling back is crucial for maintaining efficient operations. An anti-slip conveyor belt can significantly help, thanks to its specialized surface designed to enhance grip and keep products securely in place.
How to Stop Products from Slipping on Conveyors: Anti-slip conveyor belts feature an embossed, raised grip face that prevents products from slipping during transportation. This raised texture, often seen in black or green belts, provides a gripping surface that holds products firmly in position, making it ideal for conveyor systems that need to handle inclines, declines, or reversible movements.
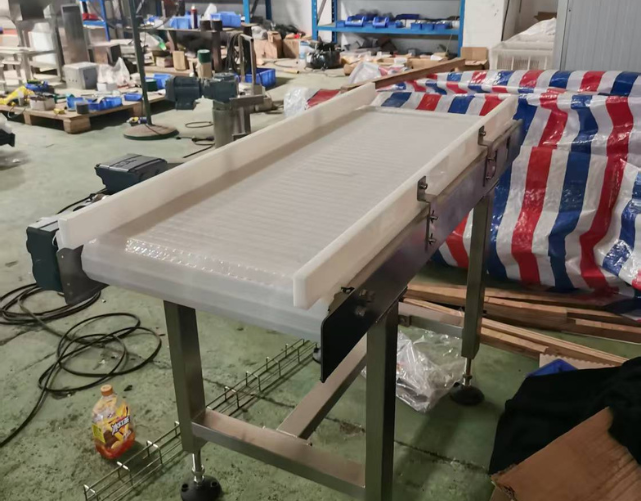
Why Choose Fill Package Modular Belt Conveyors?
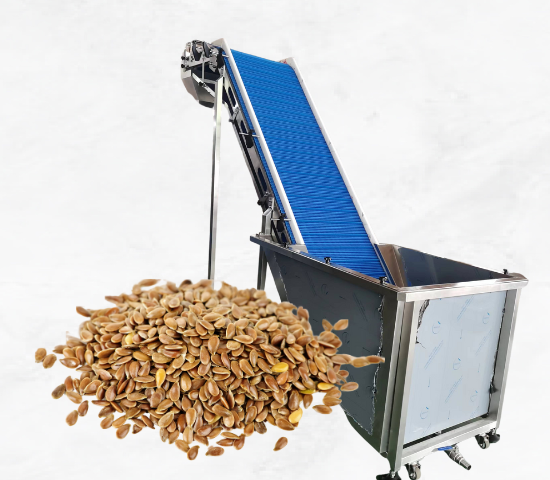
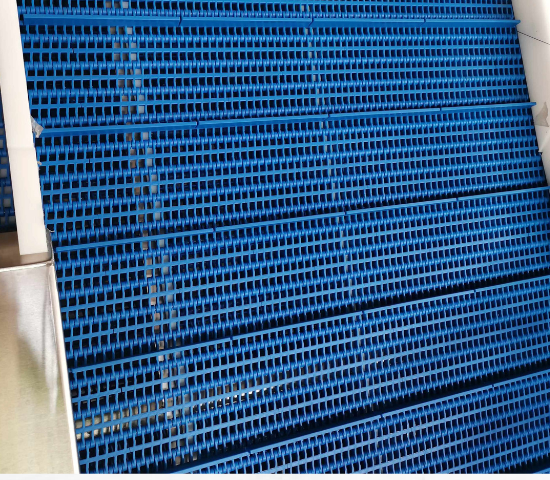
- Premium belts from leading suppliers (Xinhai modular plastic belts)
- SEW motor as standard for reliable operation
- Full welded frames for superior durability
- Custom design tailored to your factory layout and product needs
- Proven track record in food & industrial applications
- Whether you need a modular plastic conveyor belt for seafood, frozen vegetables, baked goods, or heavy industrial parts, we design systems that fit your production.
- Additionally, the positive drive mechanism of the conveyor ensures smooth operation, even when dealing with difficult length-to-width ratios. This system can also absorb lateral forces, allowing for diagonal movement of workpieces, further enhancing its versatility.
Want a Conveyor That Saves Time & Money?
Choose modular belt conveyors for lower maintenance, flexible application, and long-term reliability.
Modular belt conveyors are more durable, hygienic, and flexible than traditional flat belts.
-
Flat belts are prone to stretching, tearing, and are harder to clean.
-
Plastic modular conveyor belts can handle heavy loads, wet environments, and abrasive materials with less wear.
Additionally, damaged sections are replaced individually, not as a whole, which lowers long-term maintenance costs.
One of the biggest advantages of a modular conveyor system is its low maintenance:
-
Damaged modules can be replaced independently.
-
No need to replace the entire belt for minor issues.
-
Self-locking design allows quick disassembly and reassembly.
This reduces downtime and spare parts expenses, especially compared to fabric belts.
Yes.
Plastic modular conveyor belts are made from food-grade materials like PP, PE, or POM, which are resistant to moisture, chemicals, and corrosion.
The open hinge structure allows easy cleaning and sanitation, making them ideal for seafood, meat, vegetables, bakery, and frozen food industries
Absolutely.
Modular belt conveyors are highly adaptable:
-
For inclines, friction top modules prevent product slippage.
-
For curves, modular links maintain belt integrity while navigating direction changes.
They are often used in factories with space constraints or complex production flows.
-
Food processing & packaging (meat, seafood, vegetables, bakery)
-
Frozen food & cold chain logistics
-
Bottling and beverage lines
-
Industrial parts conveying
-
Washing, cooling, and drying processes
Their durability and versatility make them a preferred choice across these sectors.
Different modular conveyor components (flat top, flush grid, raised rib, etc.) allow you to customize the conveyor for your product’s needs:
-
Drainage, grip, product stability, accumulation—all handled by choosing the right belt type.
This ensures smooth handling, minimal damage, and high efficiency.
Yes.
At Fill Package, we design modular conveyor systems based on:
-
Your factory space
-
Product type and weight
-
Required throughput
-
Connection with existing equipment
Incline, decline, curve, width, length—every detail is customized for you.
-
Standard modular conveyors: 20–25 working days
-
Custom-designed systems: 30–35 working days, depending on complexity
Our production ensures a balance between speed, quality, and precision.