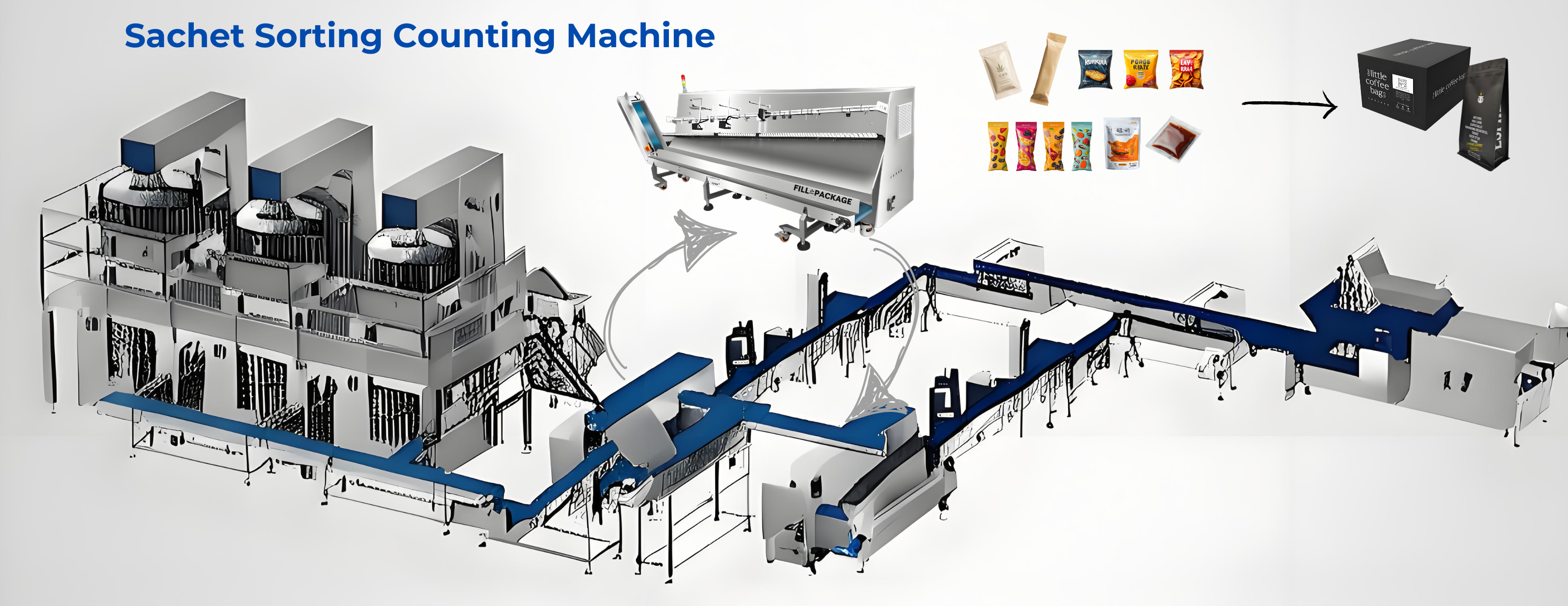
Automatic Sachet Counting Machine: Optimize Your Packaging Line with High-Speed Sorting
In automated packaging lines, small packaged products-Sachet (bags, strips, and small items) often enter the process in a disorganized and scattered manner. Traditional manual sorting is slow, costly, and prone to errors.
The Sachet Counting Machine is designed to efficiently sort, align, and organize scattered small packages, ensuring they are neatly arranged and accurately fed into packaging machines, cartoners,conveyor,Flow wrapper etc .. This improves efficiency, stability, and automation in your production line.
✅ Automated Sorting & Precise Alignment – Organizes scattered small packages for consistent, high-quality packaging.
✅ High-Speed Performance – Handles bags, strips, and small items at 80-300 packs per minute.
✅ Precision Control – 10-20 servo motors + optical sensors ensure smooth, slip-free operation.
✅ Reduced Labor Costs – Cuts 4-6 manual workers, saving $50,000+ per year.
✅ Works with Different Packaging Machines– Compatible with cartoners, flow wrappers, pouch packaging machines, X-ray, and metal detectors.
📌 Ideal for vacuum-packed food (ready-to-eat, snacks, sauces), pharmaceuticals, and personal care products.
Workflow Overview -Sachet Sorting &Counting machine (3)
The working process of the sachet sorting machine typically follows these key steps:
1.Material Feeding -Randomly scattered sachets are fed into the sorting system via a conveyor belt or vibratory bowl feeder. The purpose of this stage is to deliver a continuous flow of sachets to the machine for inspection and sorting.
2.Dectction,As sachets enter the sorting area, advanced sensors—such as photoelectric sensors or vision inspection systems—detect their position, orientation, and shape. The system instantly analyzes whether each sachet is correctly aligned or requires adjustment. Using this real-time data, a servo-controlled mechanism adjusts the sachet’s position to match the required orientation for packing.
3.Sorcting . the sachets pass through a mechanical alignment system, which can include rotating rollers, pneumatic arms, or robotic actuators. These components gently reposition and align the sachets according to preset rules—such as facing the same direction, spacing them uniformly, or arranging them into rows. This stage ensures a neatly organized line of sachets, ready for accurate counting or packaging.
4. Next ….Once properly sorted and aligned, the sachets are transferred smoothly to the next stage—typically an automatic packaging machine, cartoning machine, or multi-lane counting system. The seamless integration ensures a continuous, uninterrupted workflow that supports high-speed and high-accuracy automation.
Material Input - Automatic Sensing & Adjustment
- Scattered sachets puted into the large-capacity storage hopper.
- Photoelectric sensors detect material levels and automatically adjust the conveying speed.
- Inclined conveyor feeding dynamically adjusts speed based on material quantity, preventing blockages and ensuring smooth flow.
- Multi-stage feeding system prevents pressure buildup, avoiding sachets from squeezing and affecting sorting efficiency.
📌 Advantages:
✅ Automatic material sensing → Reduced manual intervention, increased efficiency
✅ Cyclic reuse → Excess materials fall back into the hopper for reprocessing
.
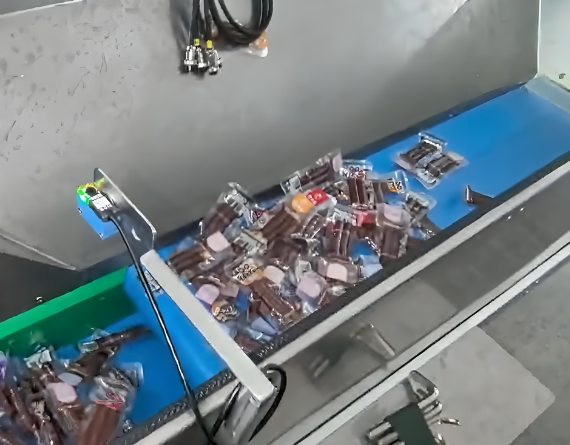
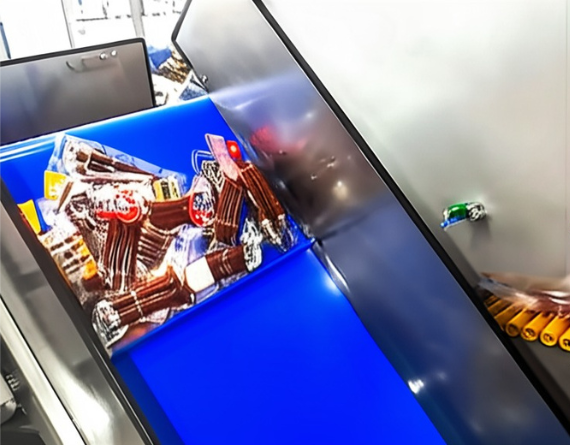
Conveying System - Photoelectric Control & Roller Sorting
- Photoelectric-controlled conveyor feeding → The system detects the material level and ensures smooth, even feeding.
- Storage hopper conveyor system uses photoelectric sensors + system-controlled actions to precisely transport materials to the lifting unit and lateral distribution unit.
- Small-diameter rollers (min φ10mm) keep materials close to the surface, preventing flipping or misalignment.
- High-adhesion silicone belts ensure sachets don’t slip or jump, keeping them in position.
📌 Advantages:
✅ Automated feeding control → Smart material handling
✅ Stable and precise transport → No sachet flipping or misalignment
Multi-Stage Sorting - Separation, Alignment & Spacing Adjustment
- Materials pass through low-speed → medium-speed → high-speed rollers in sequence.
- Differential roller system:
- Front-end slow rollers guide sachets into sorting channels.
- Mid-speed rollers accelerate to create spacing and prevent overlapping.
- High-speed rollers align sachets into an orderly sequence for downstream processing.
- Sorting rollers have an automatic rejection system to eliminate misaligned or excess sachets, sending them back to the hopper for reuse.
📌 Advantages:
✅ Step-by-step acceleration → Prevents jamming and congestion
✅ Recycling system → Excess materials return to the hopper for reuse
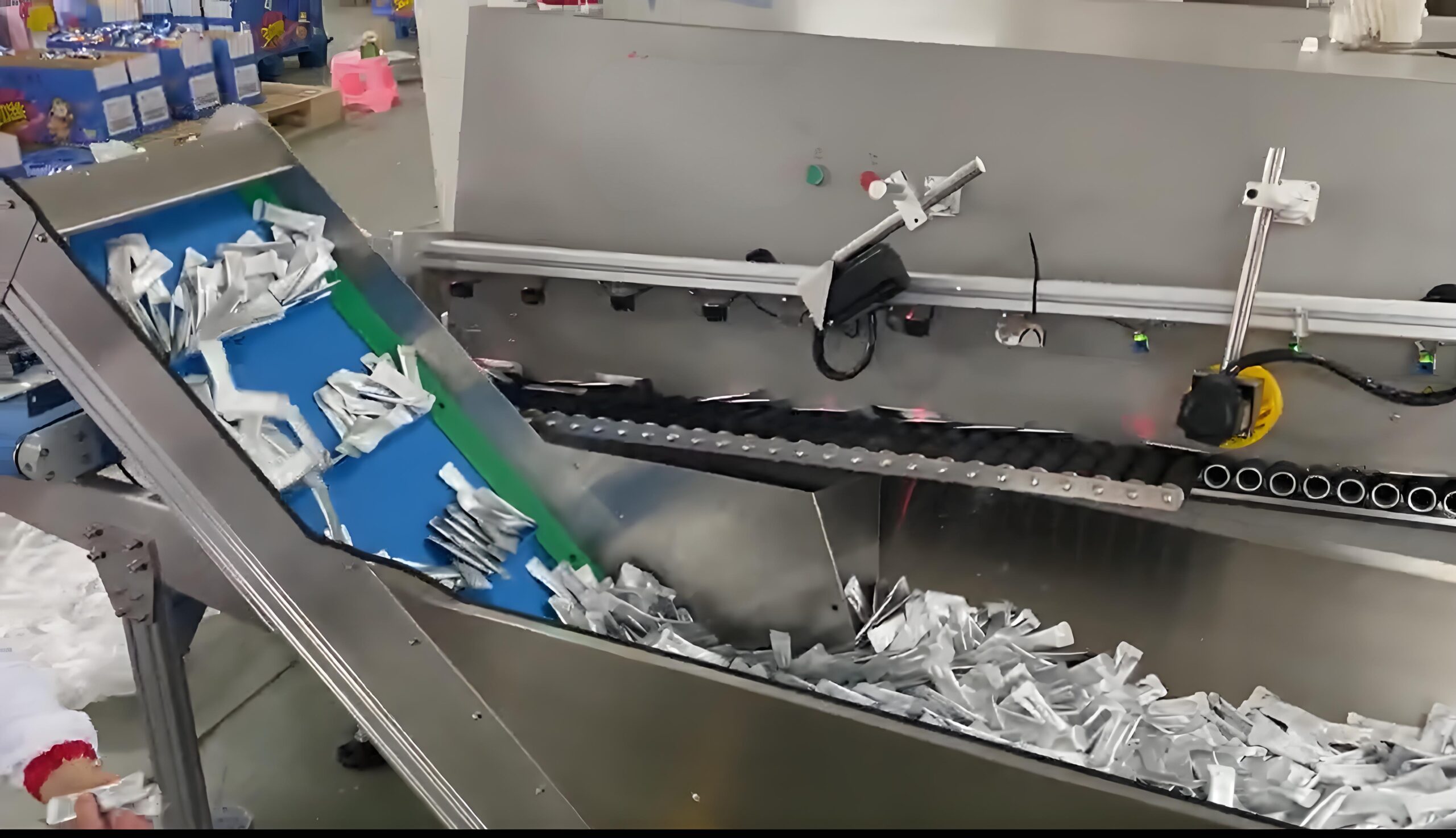
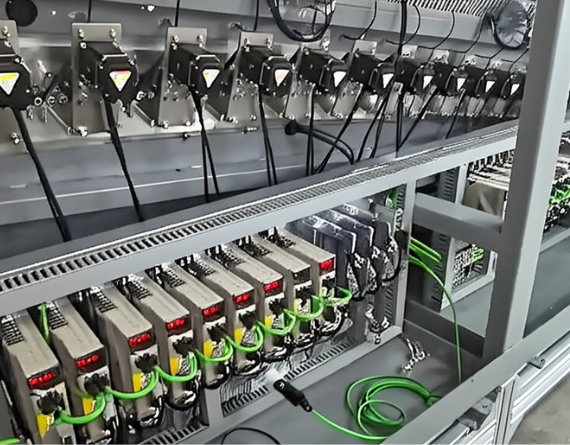
Precision Control - Servo Motor & Photoelectric Sensors
- Photoelectric sensors detect sachet position and spacing in real time.
- 16-20 servo motors independently control rollers, adjusting speed dynamically.
- Differential servo control: If a sachet shifts or overlaps, the system compensates by adjusting speed.
- Motion control system fine-tunes each roller’s torque to prevent sachets from slipping or getting stuck.
📌 Advantages:
✅ Servo control → More precise than stepper motors, no step loss
✅ Photoelectric + motion control system → Intelligent real-time adjustment
Output - Transport sachet to the next packaging machine.
- Final alignment adjustment: High-speed rollers maintain uniform spacing and orderly arrangement.
- Compression device:
- First-stage compression barrier flattens stacked sachets before they proceed to final sorting.
- Prevents multiple sachets from sticking together, ensuring smooth packaging.
- Mechanical rejection system:
- Servo-controlled mechanical ejection removes non-conforming sachets (more precise than air-blowing methods).
- Prevents defective sachets from entering the packaging machine, ensuring product quality.
- Sorted sachets are fed into cartoners, bagging machines, or packaging machines for the next stage.
📌 Advantages:
✅ First-stage compression → Reduces sachet overlap, improving sorting accuracy
✅ Precision rejection system → Enhances product quality
✅ Orderly output → Improves downstream machine efficiency
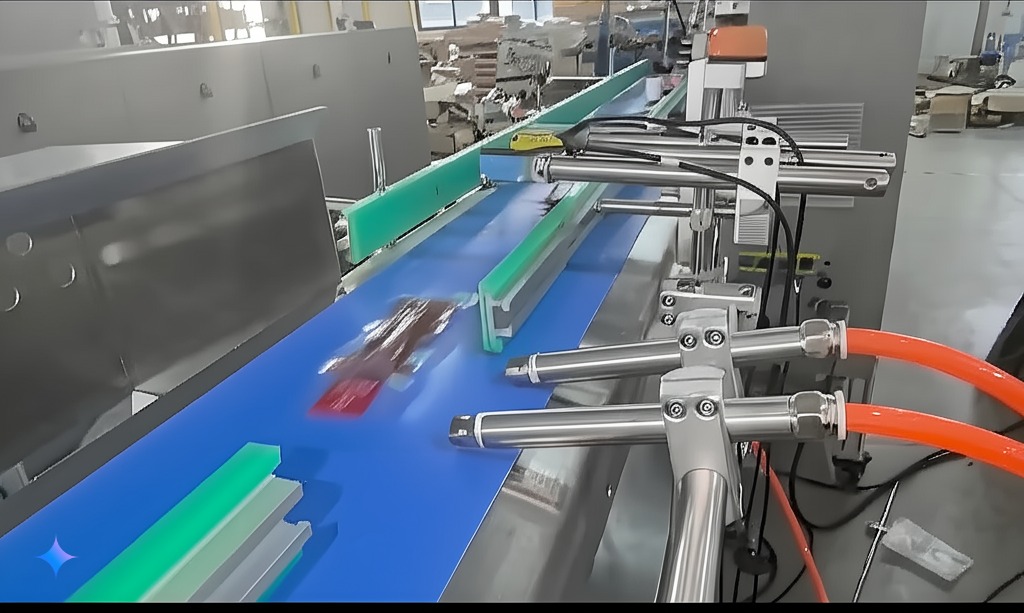
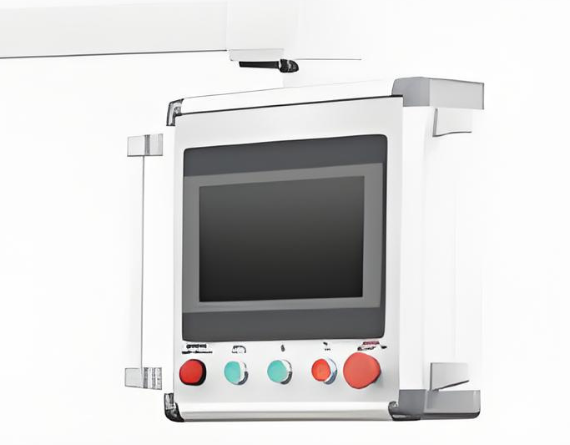
HMI- Customizable Software & Remote Suppor
- User-friendly HMI for quick adjustments and real-time monitoring.
- Proprietary software allows customization to meet specific needs.
- Built-in remote module for overseas support, enabling fast troubleshooting and reducing downtime.
📌 Advantages:
✅ HMI for easy operation → No complex training required
✅ Customizable software → Adapts to different product requirements
✅ Remote support → Faster issue resolution, lower maintenance costs
📌 Why Choose Our Automatic Sachet Counting Machine?
💡 Faster – Designed for small packaged products, efficiently sorts Max 300 packs per minute.
💡 More Precise – Small-diameter rollers (12mm) + 16-20 servo motors, ensuring smooth, jam-free operation.
💡 More Cost-Effective – Reduces 4-6 manual workers, saving $50,000+ per year.
💡 More Stable – Runs 24/7 without failures, easy to maintain, and built for long-term durability.
💡 Smarter Operation – self-diagnosis technology, detecting 98% of common faults and displaying solutions on the HMI touchscreen.
💡 Highly Compatible – Easily integrates with cartoners, flow wrappers, pouch packaging machines, X-ray, and metal detectors.
💡 Food-Grade & Safe – Made from 304 stainless steel, compliant with HACCP & GMP standards.
💡 Excellent After-Sales Support – on-site installation, operator training, remote technical assistance, and fast spare parts supply.
Applicable Packaging Types
The sachet counting machinery is widely used in sachet packaging systems, organizing scattered materials into an orderly manner before sending them into packaging bags. This is commonly used in industries such as food, pharmaceuticals, and cosmetics. The applicable types of sachets include:
- Flat Pouches: Standard pouch type, suitable for various materials.
- Stand-up Pouches: Used for more rigid materials, ensuring the pouch remains stable and easy to stack.
The sachet sorting counting machinery can send sorted materials into box packaging systems, suitable for industries like electronics, hardware, and cosmetics. Common types of box packaging include:
- Paper Boxes: Suitable for most lightweight items, easy to stack and store.
- Plastic Boxes: Used for items that require additional protection, such as electronic components or small tools.
According to customer-specific requirements, sachets counting machinery can also work with other special packaging equipment to provide customized packaging. For example:
- Aluminum Foil Pouch Packaging: Commonly used for products that require higher packaging standards, such as chemicals ,tea and pharmaceuticals.
- Foam Packaging: Suitable for fragile items that require additional protection.
Related Product
📞 Contact us now for your customized solution!
📌 Do you also face problems like slow manual sorting, high costs, and packaging unable to keep up with production capacity?
📌 Contact us for a free test of your product and see the sorting results!
✅ The machine can process 800-1,200 pieces per hour, depending on the size and shape of the materials.
✅ For fragile or irregularly shaped items, the belt speed (0.3-1.2 m/s) can be adjusted to ensure smooth and gentle handling.
✅ Suitable for bags, strips, and small items, meeting various production needs.
✅ Food Packaging (vacuum-packed snacks, sauces, seasoning sachets, coffee, tea bags)
✅ Pharmaceutical & Medical (test kits, granules, powdered medicines, capsules)
✅ Personal Care (face masks, wet wipes, laundry detergent pods)
✅ Tea & Coffee (individually packed tea bags, instant coffee sachets, beverage powder packs)
✅ Operating Temperature: 0-40°C
✅ Humidity: 30-85% RH (non-condensing)
✅ Storage Temperature: -20°C to 60°C
✅ Compressed Air Pressure: 0.6-0.8 MPa
✅ Air Consumption: 0.5 m³/min
✅ Filtration System: Equipped with a three-stage filtration system and an adjustable oil mist lubricator to ensure stable operation.
🔹 Routine Inspections: 12 daily checks, 8 monthly maintenance tasks, 5 annual overhauls to ensure optimal performance.
🔹 Key Component Maintenance:
- Servo motor bearings need lubrication every 2,000 operating hours.
- First gearbox oil change after 500 hours, followed by regular maintenance.
🔹 Self-Diagnosis System: - Automatically detects 98% of common faults.
- Displays troubleshooting solutions on the HMI touchscreen, making maintenance easier and reducing downtime.
.
✅ The machine is highly versatile and can be integrated with various packaging equipment, including:
✔ Cartoners
✔ Flow Wrappers
✔ Pouch Packaging Machines
✔ X-ray Inspection Systems
✔ Metal Detectors
✅ Yes, the machine is designed to handle various sizes and shapes of sachets, strips, and small items.
✅ Servo motors and optical sensors automatically adjust conveyor speed and positioning.
✅ Quick and easy format change, adapting to different product requirements.
✅ User-friendly interface, with a touchscreen HMI for easy operation.
✅ One-touch adjustments, allowing quick format changes.
✅ Operator training provided, ensuring smooth operation and minimizing downtime.Even ,Remote control
✅ Yes! We offer global after-sales support, including:
✔ Remote technical assistance (phone/video guidance)
✔ On-site installation, setup & training
✔ Regular maintenance & spare parts supply
✔ Free software updates to optimize performance