Hopper Feeder: Elevate Your Material Handling Efficiency
Overview
The Hopper Feeder is a sophisticated solution designed to streamline bulk product loading, enhance in-process storage, and ensure uniform feeding to scales or other processing systems. This feeder is ideal for food processors and other industries requiring efficient, safe, and reliable material handling.
Why Our Hopper Feeder?
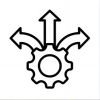
Automates material handling, reducing labor costs and enhancing throughput.
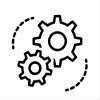
Provides a steady and uniform supply of materials, improving product quality.
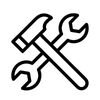
Adaptable to various industrial applications and specific requirements
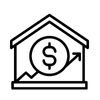
Lowers the risk of injuries associated with manual material handling.
What is a Hopper Feeder?
A hopper feeder operates on a simple yet effective principle. It holds material, such as bulk products in industrial settings, and uses gravity to dispense it into a tray or conveyor system. As the material is consumed or processed, the hopper automatically replenishes the bottom tray, maintaining a steady supply without the need for constant manual intervention.
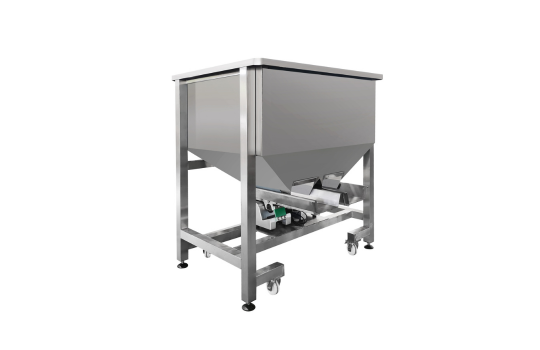
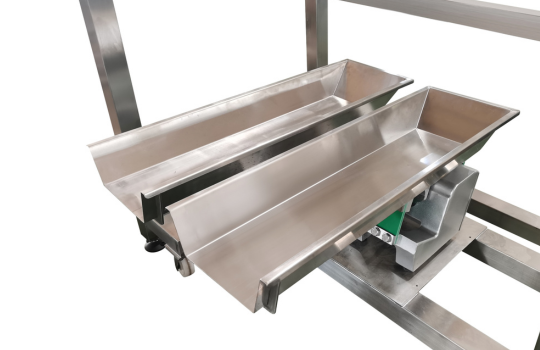
Vibrating Feeder Hopper Key Features
- Optimized Efficiency: Enhances the flow of materials, reducing manual intervention and increasing productivity.
- Safety: Improves workplace safety by minimizing the need for manual handling of bulk materials.
- Customizable Design: Tailored to meet specific operational requirements, including size, material type, and output rate.
- Robust Construction: Engineered with high-quality materials to endure demanding industrial environments.
- Ease of Maintenance: Designed for easy access and maintenance, ensuring minimal downtime
Vibration Feeder Hopper Application
Hopper feeders are widely utilized in various sectors, such as:
- Food Processing: Ensuring consistent feeding of bulk ingredients and products to processing lines and scales.
- Manufacturing: Handling raw materials and components efficiently in production environments.
- Agriculture: Distributing seeds, fertilizers, and livestock feed.
- Packaging: Managing product flow in packaging lines for increased efficiency.
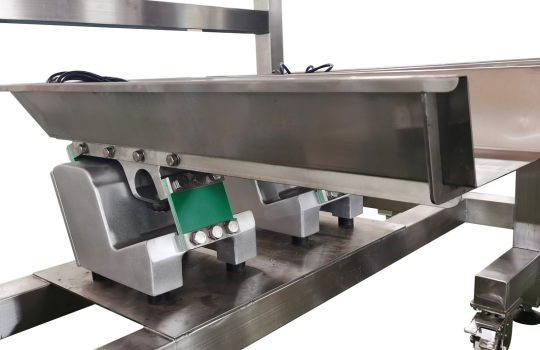
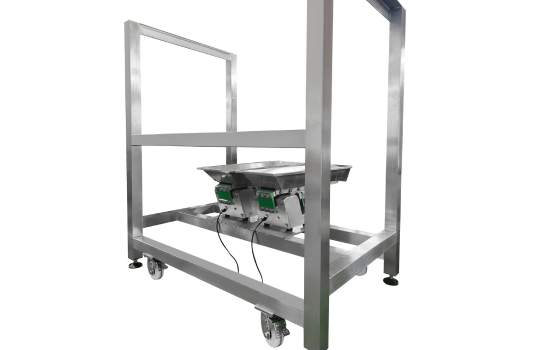
How to Design a Hopper Feeder
Designing a hopper feeder involves several crucial steps:
- Selecting the Right Size and Material: Choose appropriate dimensions and materials based on the type and volume of material to be handled.
- Determining Output Rate: Set the desired output rate to ensure the feeder meets production needs.
- Constructing Components: Build the hopper and other necessary components to facilitate smooth material flow.
- Ensuring Smooth Operation: Design the system to prevent clogging and ensure continuous material movement.
Vibratory Feeder Design
Vibratory feeder design is crucial for achieving optimal performance. The design should ensure efficient material movement, minimize maintenance requirements, and be tailored to the specific needs of the application. Key considerations include the type of materials handled, desired output rate, and operational environment.
Vibratory Feeder Working Principle
Vibratory feeders operate on the principle of creating controlled vibrations to move materials. This is typically achieved using an electromagnetic drive or a mechanical drive system. Here’s how it works:
- Drive System: The vibratory feeder is equipped with an electromagnetic or mechanical drive that generates vibrations. The drive system’s frequency and amplitude are carefully controlled to achieve the desired material flow rate.
- Tray Movement: The vibrations are transferred to the feeder tray. As the tray vibrates, it moves the material along its surface. The amplitude (the height of the vibration) and frequency (the speed of the vibration) can be adjusted to control the flow of materials.
- Material Movement: The material is moved forward by the vibrations. On an electromagnetic vibratory feeder, the rapid vibrations cause the material to move in a series of small jumps along the tray surface. On a mechanical feeder, the motion is typically slower but with larger jumps, suitable for moving heavier or bulkier materials.
- Controlled Flow: The design of the tray and the vibration settings ensure that the material moves at a consistent and controlled rate. This allows for precise feeding into processing equipment, maintaining a steady flow without blockages or interruptions.
- Adjustability: Vibratory feeders can be adjusted to handle different types of materials and flow rates. The amplitude, frequency, and angle of deflection can be modified to suit specific process requirements.
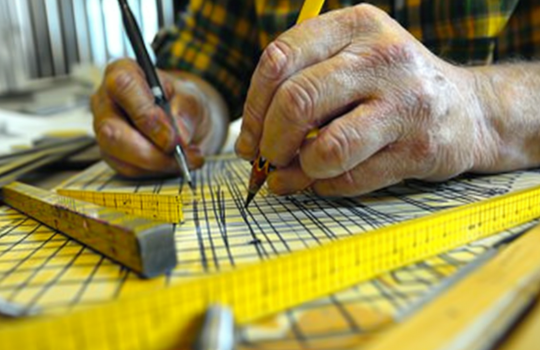
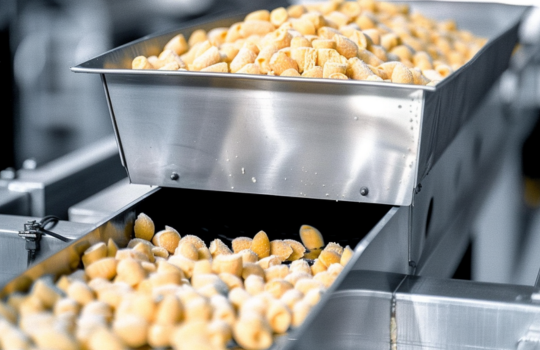
Why Choose Our Hopper Feeders?
Our hopper feeders are crafted to deliver unmatched reliability and performance. We offer customized solutions to fit your specific needs, supported by exceptional customer service. Whether you require a standard model or a bespoke system, our team of experts is dedicated to helping you optimize your material handling processes.
Choosing the Right Feeder
Different types of vibratory feeders are suited for various applications:
- High-Speed Feeders: Ideal for applications requiring fast travel speeds and frequent start-stop operations.
- High-Amplitude/Low-Frequency Feeders: Best for handling light and bulky materials like cereals, spices, and snacks.
- High-Stroke Mechanical Conveyors: Suitable for high-capacity applications with longer conveying distances.
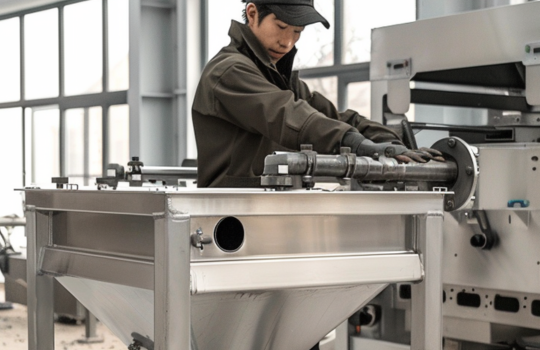
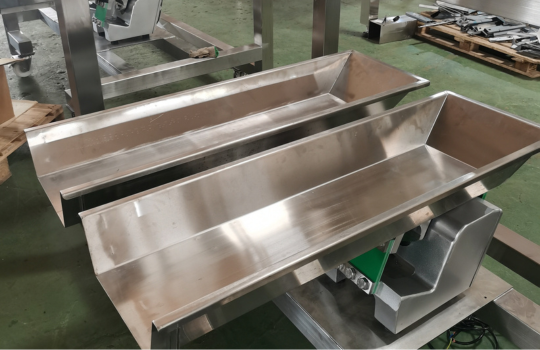
Electromagnetic Feeders vs. Mechanical Feeders
Electromagnetic feeders are ideal for continuous or on/off operations and can adjust to changing process requirements. Electromechanical feeders are well-suited for continuous operations requiring low-frequency and high-amplitude movement. Both types offer unique advantages depending on the specific application needs.
Customizable Tray Designs
Modern feeder and conveyor trays can be customized in shape, length, and width to meet unique process requirements. Options include flat, curved, v-channel, and tubular designs, with quick-release features for easy cleaning and maintenance.
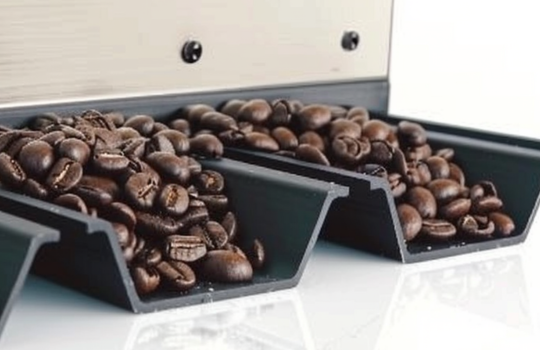
Feature Box
Specification | Details |
---|---|
Hopper Capacity | Customizable based on needs |
Material Construction | Options include stainless steel, aluminum, and other durable materials |
Output Rate | Adjustable to suit production requirements |
Feeding Mechanism | Gravity-fed, with options for motorized feeding |
Applications | Food processing, manufacturing, agriculture, and more |
Safety Features | Includes safety guards and easy maintenance access |
Customization | Fully customizable design to meet specific industry needs |
Hopper feeders are essential for efficient and safe material handling across various industries. They provide reliable, consistent, and automated feeding of bulk materials, significantly enhancing productivity and reducing operational costs. Investing in a high-quality hopper feeder is a strategic decision for any organization aiming to streamline its material handling operations.
Hopper feeders can manage a variety of materials, including bulk food products, raw materials, livestock feed, seeds, and fertilizers.
By automating the loading and feeding process, hopper feeders reduce manual handling, increase throughput, and ensure a consistent material flow.
Yes, hopper feeders can be tailored in terms of size, material construction, output rate, and feeding mechanism to meet specific operational requirements.
Hopper feeders are designed with integrated safety guards and easy maintenance access to enhance workplace safety.
Industries such as food processing, manufacturing, agriculture, and packaging benefit greatly from the use of hopper feeders.
Hopper feeders use gravity or motorized mechanisms to ensure a steady and uniform flow of materials, enhancing product quality.
The capacity of hopper feeders varies based on design requirements and can be customized to meet specific needs.
Hopper feeders are designed for easy maintenance, with accessible components and safety features to ensure minimal downtime.
Related Product
How to install the bucket elevator ?
Follow is some details to take a note .
Open the wooden box and take components out. Release the cover plate and the motor fixing bolts, and release the electric motor tooth chain .
Fix the side plates on the top of the pedals on both sides, each sharing a parallel serial number, only, and tie the two side plate connectors on top. 4 PCS are net fixing bolts m10x20, and 4 pieces are m10x25. be careful, counter loading may be encountered against the outer edge of the bunker.
The sprocket is located at the front of the top of the elevator, and the rubber sprocket with cushion is placed on the left side. The bolts should be placed on the two sprockets corresponding to the local area, as shown. Fix the top sprocket on the back: there should be a hole for the rubber band
Fixed chain, a total of two specifications of the chain, loaded in the direction of bucket elevator work, first installed with the side of the material, through the chassis last path back through the sprocket, penetration drive sprocket and tight sprocket from top to bottom
Take the storage hopper directly ,fix it with 8pcs nuts ,fixed upward allong with storage hopper